The Definitive Guide to Alcast Company
It also improves the machinability of the alloy, making it much easier to process into completed products. In this method, iron adds to the general workability of aluminum alloys. Copper raises electrical conductivity, making it beneficial in electrical applications. It also boosts rust resistance and contributes to the alloy's total toughness.
Manganese contributes to the toughness of light weight aluminum alloys and boosts workability. Magnesium is a lightweight component that offers strength and influence resistance to aluminum alloys.
Alcast Company - Truths
Zinc boosts the castability of aluminum alloys and helps control the solidification process during casting. It improves the alloy's strength and hardness.

The main thermal conductivity, tensile stamina, return strength, and elongation vary. Among the above alloys, A356 has the highest thermal conductivity, and A380 and ADC12 have the most affordable.
All About Alcast Company
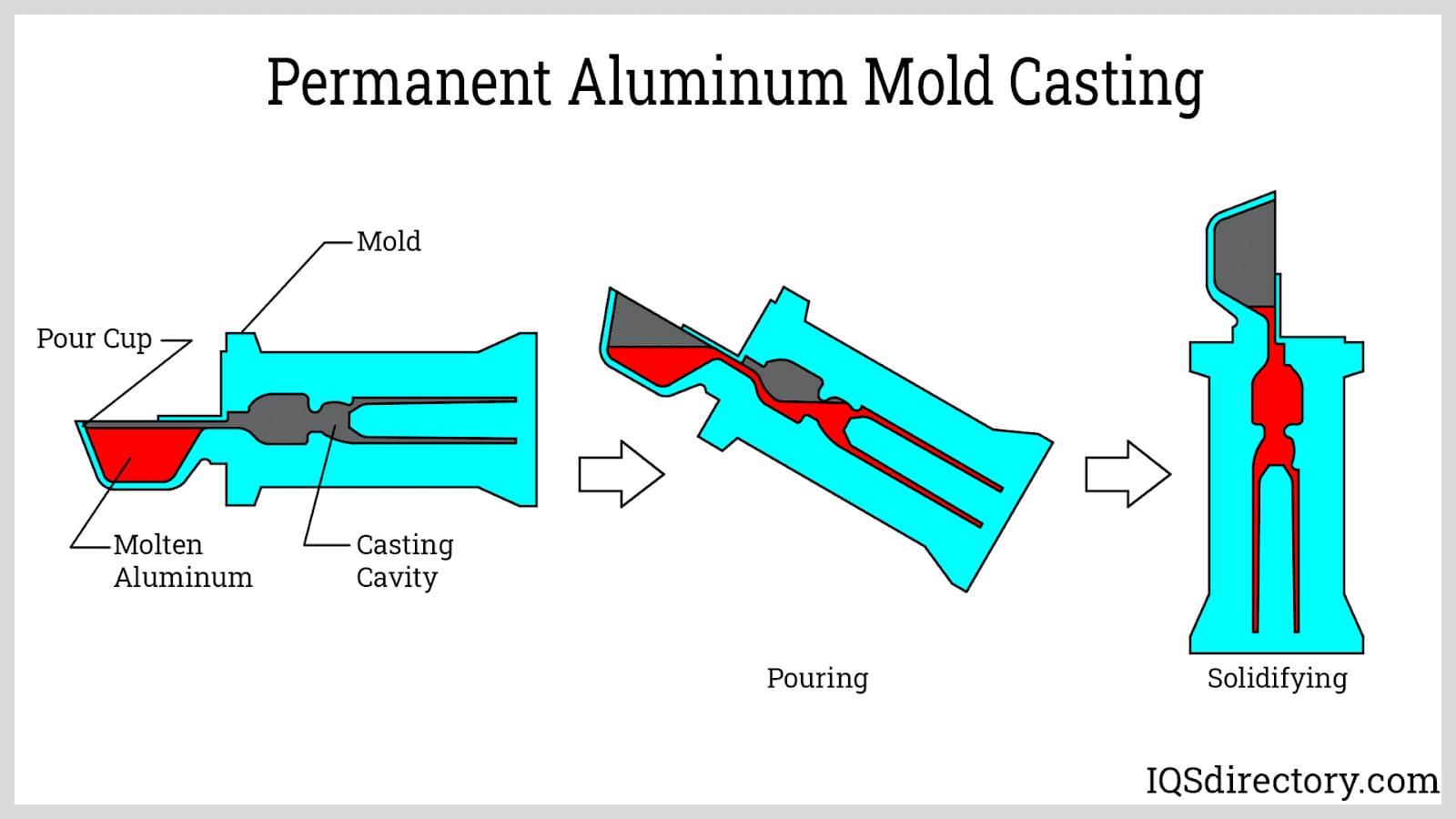
(https://profile.hatena.ne.jp/a1castcmpny/)It is a material commonly made use of in the aluminum casting industry. The bearing capability of the products produced by this material is Solid, has high mechanical residential or commercial properties, good cutting performance, excellent demolding performance, high spreading pass rate, specifically friendly for thin-walled components, and can satisfy the requirements of high-performance light weight aluminum alloy die castings.
In accuracy spreading, 6063 is well-suited for applications where intricate geometries and premium surface finishes are critical. Instances include telecommunication enclosures, where the alloy's superior formability enables for sleek and cosmetically pleasing styles while maintaining architectural honesty. In the Lighting Solutions market, precision-cast 6063 parts produce classy and effective lights components that require detailed shapes and great thermal performance.
The A360 shows superior elongation, making it suitable for complex and thin-walled parts. In precision spreading applications, A360 is fit for markets such as Customer Electronics, Telecommunication, and Power Devices.
Some Known Details About Alcast Company
Its one-of-a-kind residential properties make A360 a beneficial choice for precision casting in these markets, enhancing product longevity and top quality. aluminum metal casting. Light weight aluminum alloy 380, or A380, is a commonly utilized casting alloy with a number of distinct qualities.
In accuracy casting, aluminum 413 shines in the Customer Electronic Devices and Power Equipment sectors. It's generally utilized to craft complex elements like mobile phone housings, video camera bodies, and power device cases. Its precision is amazing, with tight resistances approximately 0.01 mm, making certain perfect product assembly. This alloy's premium deterioration resistance makes it an excellent selection for exterior applications, making certain long-lasting, sturdy products in the pointed out industries.
All About Alcast Company
The light weight aluminum alloy you select will considerably influence both the casting process and the homes of the last item. Due to the fact that of this, you must make your decision very carefully and take an informed method.
Identifying the most appropriate light weight aluminum alloy for your application will certainly suggest considering a broad selection of characteristics. These comparative alloy characteristics follow the North American Pass Away Spreading Organization's standards, and we have actually split them into two classifications. The first category index addresses alloy characteristics that affect the production procedure. The 2nd covers attributes influencing the properties of the final item.
See This Report on Alcast Company
The alloy you choose for die spreading directly impacts several facets of the casting procedure, like exactly how easy the alloy is to work with and if it is prone to casting defects. Hot cracking, likewise called solidification breaking, is a normal die spreading flaw for light weight aluminum alloys that can cause inner or surface-level splits or cracks.
Specific light weight aluminum alloys are much more at risk to hot fracturing than others, and your selection must consider this. Another typical defect discovered in the die casting of aluminum is die soldering, which is when the actors sticks to the die walls and makes ejection tough. It can harm both the cast and the die, so you ought to try to find alloys with high anti-soldering buildings.
Rust resistance, which is currently a noteworthy feature of aluminum, can vary significantly from alloy to alloy and is a vital characteristic to think about depending on the ecological problems your item will be exposed to (aluminum casting manufacturer). Use resistance is one more home frequently sought in aluminum products and can differentiate some alloys
Comments on “The 9-Minute Rule for Alcast Company”